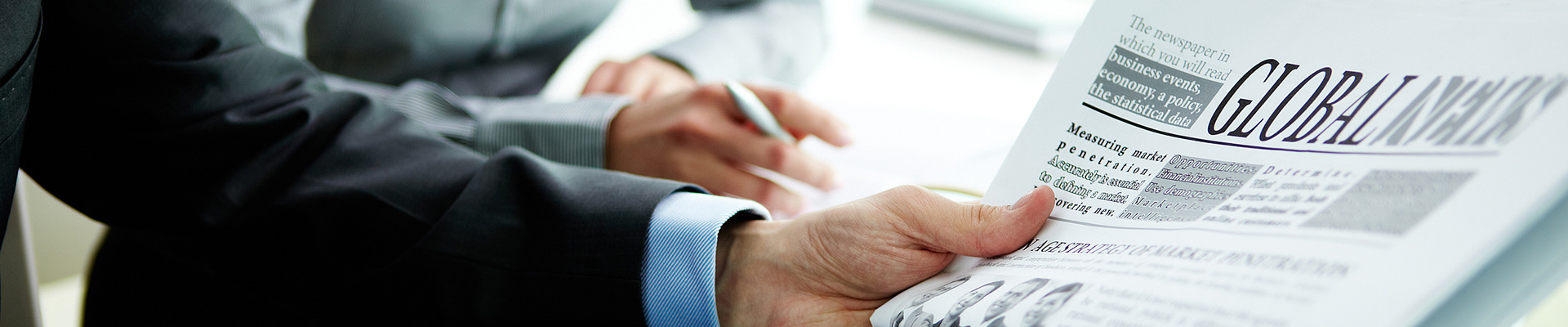
Candle filter working principle
2024-06-21 15:30

1. Fluid introduction: The fluid to be filtered is introduced into the candle filter through the inlet pipe and enters the interior of the housing.
2. Filtration: A plurality of filter elements are arranged inside the candle filter. These elements are usually cylindrical, made of ceramic or metal, and have a microporous structure. When the fluid flows through the filter element, tiny solid particles, microorganisms and other impurities are blocked by the micropores on the surface of the filter element, while the clean fluid passes through the micropores and continues to flow to the outlet.
3. Filter cake formation and filtration cycle: During the filtration process, the liquid in the slurry passes through the filter medium into the center of the porous filter element, and is collected to the clear liquid outlet for discharge. The clear liquid discharged before the candle filter does not form a filter cake is returned to the raw material slurry inlet and sent to the filter for circulating filtration until the candle filter forms a filter cake. After that, the clear liquid is no longer circulated, but is sent to the next process through the three-way valve.
Cleaning process: Over time, solid particles on the surface of the filter element will accumulate, reducing the filtration efficiency. Therefore, the filter element needs to be cleaned periodically to remove the accumulated solid particles. The cleaning system can be carried out in different ways, such as backwashing, chemical cleaning or mechanical cleaning.
5. Backblowing and slag discharge: when the filter cake on the porous candle core reaches a certain thickness, a signal will be provided to control the feed stop, then the residual liquid in the filter will be drained, and then the backblowing will be carried out to make the filter cake fall off. After a certain period of back blowing, stop the back blowing and open the slag discharge port of the filter for slag discharge. After the slag discharge is completed, close the slag discharge port and return to the initial state before filtration to prepare for the next round of filtration.
Previous article
Next article
Related News